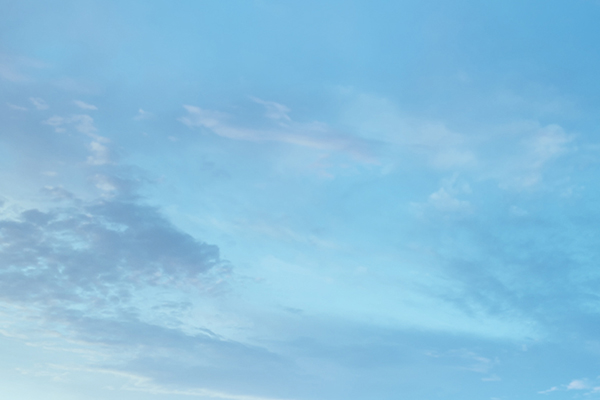
VOC removal that reduces energy consumption compared to thermal oxidation. A compact way to reduce carbon footprint and save in energy costs.
VOC removal that reduces energy consumption compared to thermal oxidation. A compact way to reduce carbon footprint and save in energy costs.
Volatile organic compounds (VOCs) are chemicals that constitute one of the primary elements of air pollution in a wide range of industries – especially in processes that use large amounts of solvents or produce carbon monoxide, or odors. VOC emissions are significant greenhouse gases, and therefore regulated by national and European directives.
Genano VOC series are state-of-the-art compact catalytic VOC and odor abatement systems for energy efficient control of VOC waste gases. It fulfills the requirements of the EU VOC directive.
1
No harmful byproducts like nitrogen oxides. After a catalytic oxidation we will only find vapor (H2O) and Carbon Dioxide (CO2).
2
Oxidizer’s exhaust air is below the EU VOC limit values. Outcoming air is free of VOCs and can be exhausted directly to outside air.
3
Saves energy because the operating temperature is nearly 500°C lower compared to thermal oxidation.
4
The lower operation temperature causes significantly less thermal stress to the constructions of the oxidizer, which directly increases the life-cycle of the oxidizer and decreases the maintenance costs.
High-end technology customized for best performance
In the video Chief Operating Officer of Genano Solutions Ville Silvonen explains how you will benefit of catalytic oxidation.
The video includes a clear calculation how Genano Catalytic Oxidizer can reduce the amount of carbon dioxide by hundreds of tons per VOC plant.
Genano’s catalytic oxidizers are fully automatic, adapting to different flow rates and different VOC concentrations.
The VOC oxidizer has been designed to enable installation outdoors or inside the production plant if preferred.
The installation area required is minimum and doesn’t interfere with other existing installations.
Genano VOC installations are always custom-designed according to your needs. Our expert team will recommend a regenerative or recuperative catalytic oxidizer installation depending on the VOC concentration.
Our specialists help to find the best solution for you by installing a new system or upgrading an existing one, sothat you can enjoy the full benefits of the Genano VOC solution year in, year out.
We provide upgrade packages to add your existing thermal oxidizer with a smart catalytic Genano VOC solution to save in operating costs.
We are happy to offer you a customized maintenance contract according to your needs.
We can provide technical support by remote monitoring for VOC oxidizer.
Even one week.
The Genano VOC system can be easily implemented into your production facility.
Simply connect your process exhaust gas pipe and chimney to oxidizer along with electricity and pressured air.
Instead of a traditional thermal oxidation, our system is based on ecological and efficient catalytic oxidation reaction.
Outcoming air is free of VOCs and can be exhausted directly to outside air.
The oxidizer contains two or three chambers operating in a regenerative mode.
1
First oxidation process - air temperature minimum 300/350°C
In the three bed technology, the contaminated air passes through the first chamber, heated up from previous operation. The air temperature is raised to minimum 300/350°C allowing the oxidation of the VOC within the catalyst.
2
The third bed of catalyst and heat exchanger mass - cool air and heated mass
In the three bed technology, the contaminated air passes through the first two chambers, heated up from previous operation. After the first oxidation process the hot air stream divides in two and passes through two different chambers with catalysts and heat exchangers, being cooled and heating the mass in the process.
3
The heating system - ensures the right temperature
If the VOC concentration of incoming air is not enough to keep the temperature above 300/350°C, then the heating system located inside the reactor will heat the air stream further for the needed time.
During the whole process the air stream is sucked by the main fan and goes through the chimney.
The outgoing air is completely treated and can be used for other heating purposes due to its temperature.
During the start-up of the VOC oxidizer and also in some situations where we don’t reach the ATP – Auto Thermal Point, additional heating energy is required.
The heating system is operated by electricity due to its ease of maintenance and required relatively small size but can be also optioned with gas heating.
The system includes a control unit by which all necessary and emergency functions of the catalytic VOC oxidizer can be controlled. The control unit is provided with all necessary inputs and outputs needed for remoting.
The system includes all instrumentation and electrical equipment needed in normal operations as well as in emergency situations.